This e-book is about glassblowing. It is noteworthy that there are no books about bronze blowing, iron blowing, or ceramic blowing, to mention three other materials that were widely used in the ancient world. Just as one can blow bubbles into a glass of water using a straw, bubbles can be blown into molten metal heated in a crucible—or even into very wet clay (slip). However, no manufacturing processes were ever developed for applying that phenomenon to the making of goods. Glassblowing “works” because of two key physical properties, simultaneously present, that are together shared by few other materials. These properties are worth noting.1
Glass...has a random molecular structure, whether the glass is cold or hot. It is often called a “super-cooled liquid” because, at room temperature, it seems to be a solid, but it has the random molecular structure of a liquid.
When, for example, metal is heated to a specific temperature, a phase change occurs. Its orderly molecular structure—crystalline—becomes random. This is the melting point, at which a solid becomes a liquid. Glass does not behave in this way. It has a random molecular structure, whether the glass is cold or hot. It is often called a “super-cooled liquid” because, at room temperature, it seems to be a solid, but it has the random molecular structure of a liquid. Odd, no? Thus, speaking practically (everything in this chapter could be described in this way because I am a glassblower and not a scientist), glass has no melting point; as it gets hotter, there is never a phase change. As glass is heated, it does something much more interesting than melting: its resistance to flow (viscosity) gradually diminishes as the temperature increases. (The temperature range in which glassblowing processes typically take place is roughly 1,300–2,100 degrees Fahrenheit [700–1,150 degrees Celsius]). At these temperatures, glass is in a “plastic” state; that is, it can be shaped easily. “Malleable” is another word used to describe its curious softness. In this state, molten glass can be stretched easily (Vid. 1).
In fact, at the most fundamental level, glassblowing is a way of stretching glass. Just as, say, tweezers can be used to pull a mass of glass to become long and narrow, compressed air can be introduced into the center of a molten mass to create and expand a bubble. The soft glass is stretched outward in all directions (Vid. 2).
This brings us to the second physical property required for glassblowing. Glass is a poor conductor of heat, compared with any metal. For glassblowing to work, the glass, as it is inflated, must hold its shape. It does so because, as the bubble grows in size, the outer surface cools rapidly and stiffens somewhat. Because glass is a poor conductor, the greater heat beneath the outer surface only slowly “replenishes” the heat at the surface. The soft bubble of glass can therefore increase in size while maintaining its form. This could not happen with metal because its greater heat conductivity would prevent the outer-wall/inner-wall heat differential required for an inflation process. In addition, as we have seen, metal exists as either a solid or a liquid. It never exhibits the “in-between” plastic state of hot glass that allows the stretching required for glassblowing.
The origins of glass made by people are…lost in the sands of time; some authorities suggest a date of about 2000 B.C., while others maintain that the proper date is some 500 years earlier.
On a timeline of glass history, glassblowing appears in about the middle. The origins of glass made by people are, it is appropriate to say, lost in the sands of time; some authorities suggest a date of about 2000 B.C., while others maintain that the proper date is some 500 years earlier. The earliest fairly closely datable glass that unequivocally exhibits signs of inflation was made between about 50 and 40 B.C.2
During the 1971 excavation of a mikvah (ritual bath) in the Jewish Quarter of Old Jerusalem, debris from a glassworking workshop was found. This included blue glass tubes with a bulge at one end (Fig. 13). The bulges were made by heating one end of the tubes to the point of softening and closing, then immediately blowing into the other end (Vid. 3). Also found were small vessels with spiraling threaded decoration made by blowing. Until some earlier evidence is discovered, these remain the oldest artifacts made by glassblowing.3
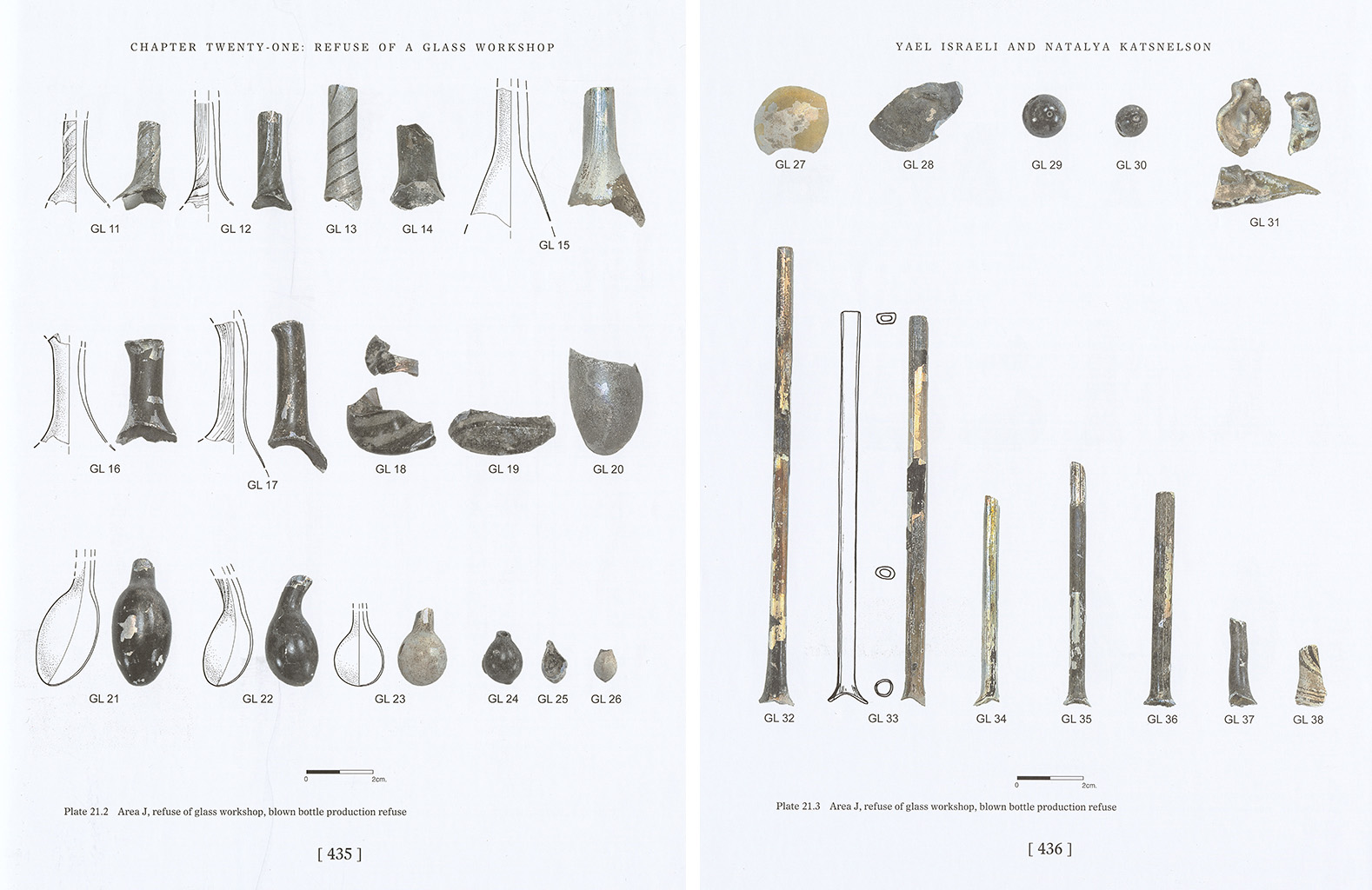
Since the opening of The Studio of The Corning Museum of Glass in May 1996, I have given countless tours of the older historical glass in the collections. After I explain our current understanding of glassblowing’s origins, someone usually asks, “So what’s the oldest piece of blown glass we see here?” This is an excellent question, and one that I always welcome. I invariably point out two possibilities, quickly adding the proviso that no one can say for sure.
The first possibility is a small, thin-walled bottle, nearly weightless in the hand, made of transparent purple-brownish glass (Fig. 14). As will be shown in Video 5, it has the hallmarks of glassblowing. This vessel closely resembles a slightly taller one that is housed in The Israel Museum in Jerusalem (Fig. 15). It is difficult to overstate the importance of this little bottle, which was found in the 1961 excavation of a cemetery in the Judean desert. The associated settlement at Ein Gedi seems to have been abandoned before 37 B.C. Therefore, the bottle is one of the earliest closely-datable complete objects made by glassblowing. To my eyes and hands (I have closely examined both vessels), the Corning and Ein Gedi bottles may have come from the same workshop.4
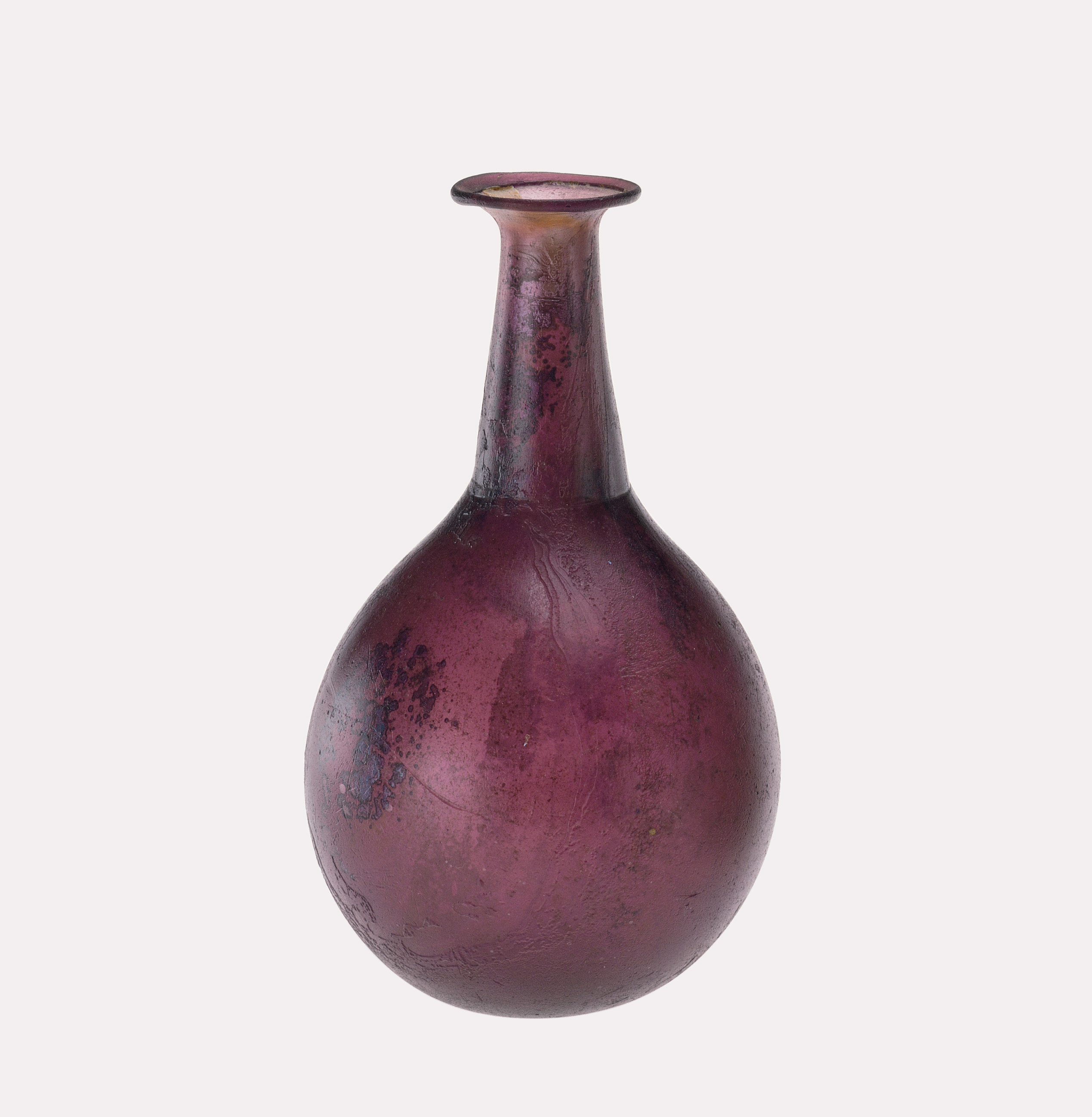
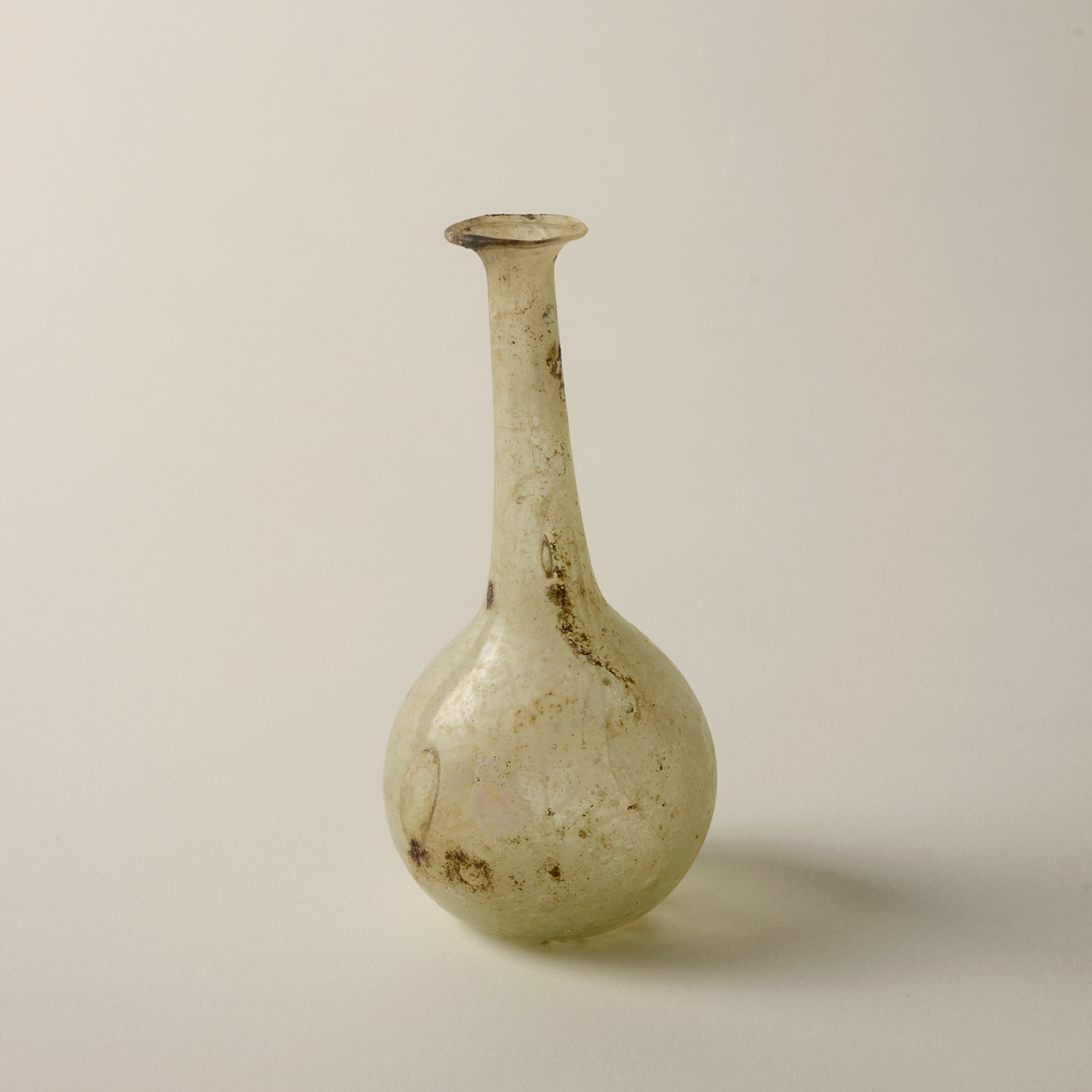
The second possibility is Corning’s Morgan Cup (Fig. 16), an ancient Roman cameo glass. It is so named because it once belonged to the American financier John Pierpont Morgan. Made from a gather of transparent dark blue glass overlaid with opaque white glass, the undecorated blank was fashioned by glassblowing. After it had cooled, lapidary workers—undoubtedly the same artisans who created items from hardstones—cut away white glass to create the mythological scenes that encircle the cup.
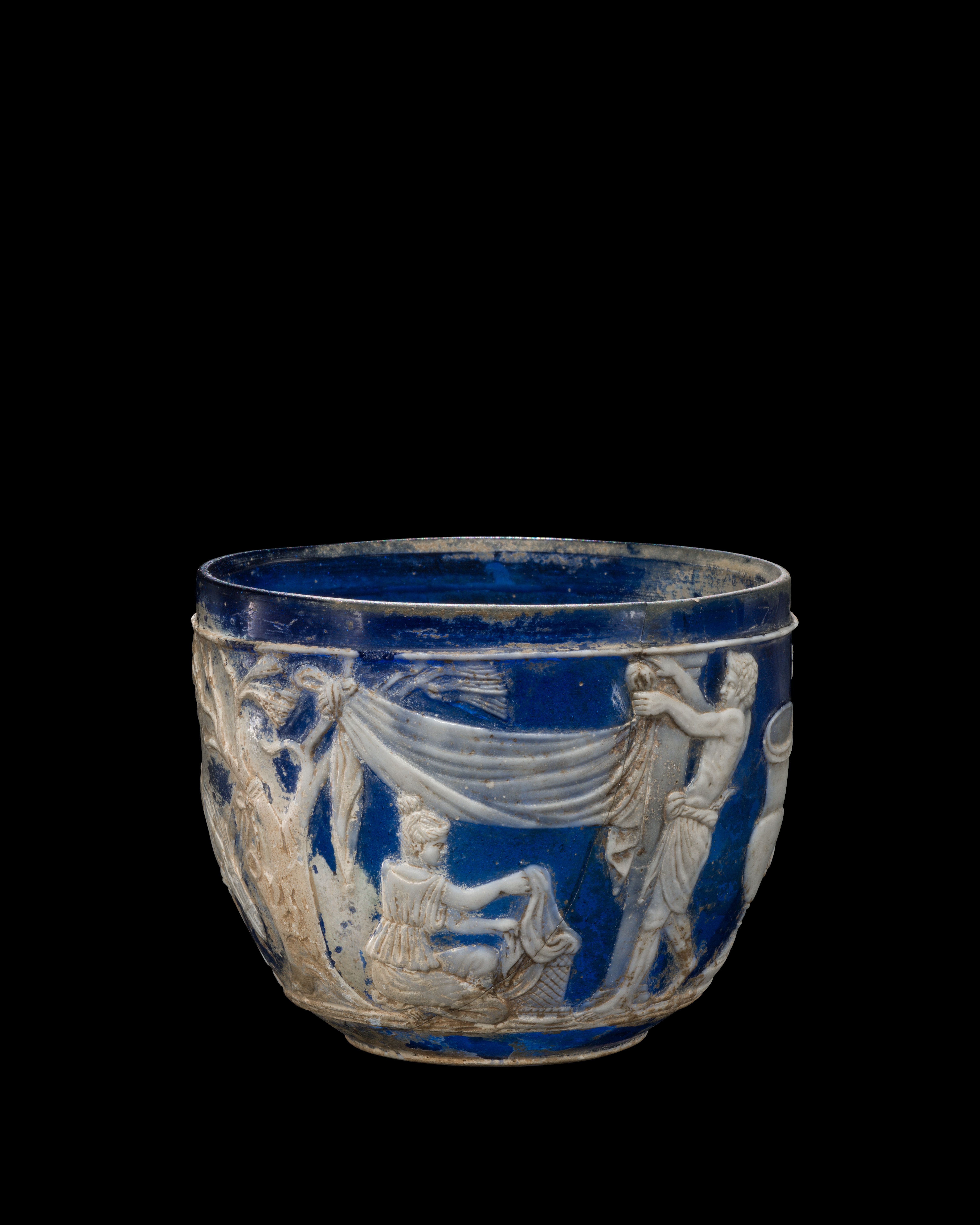
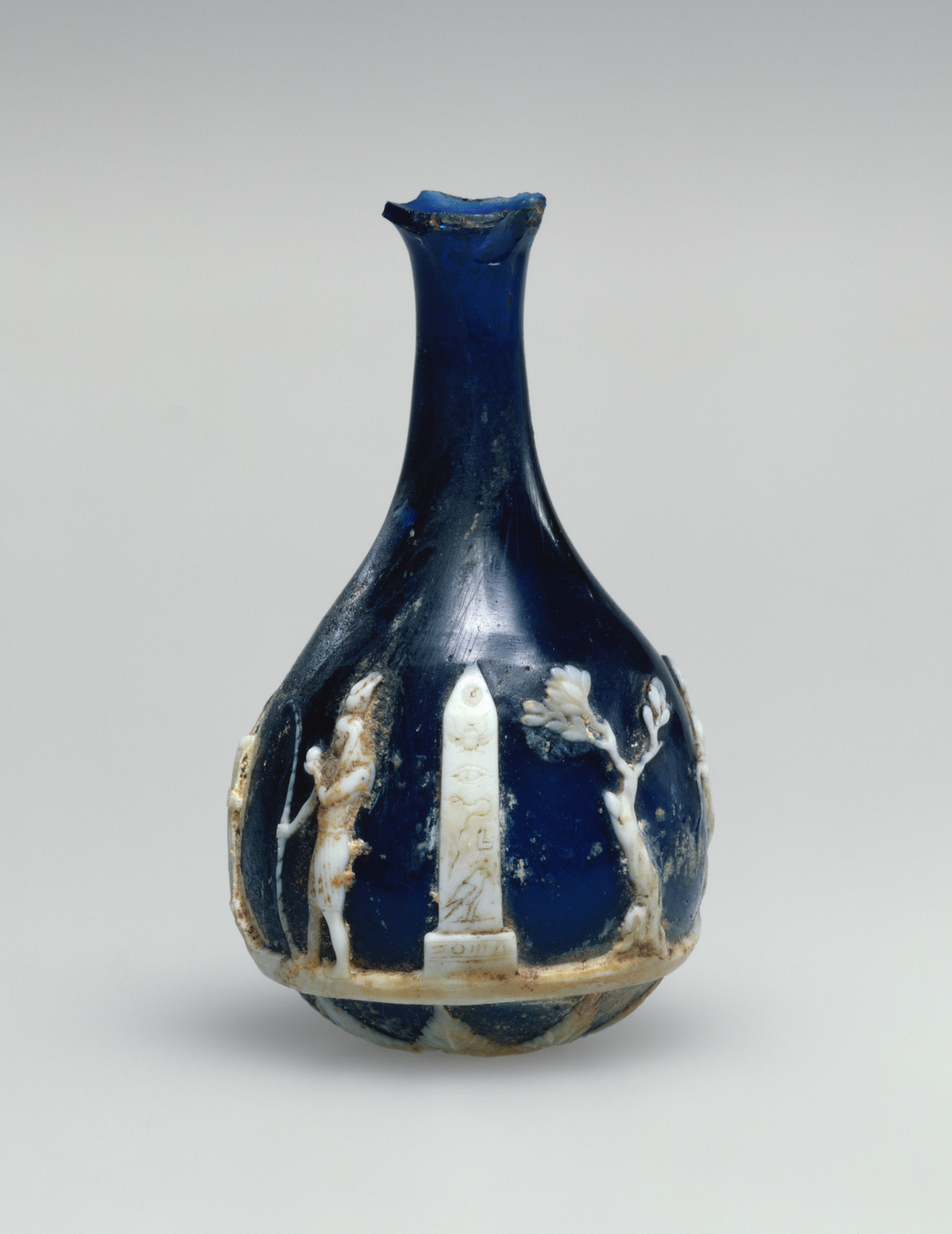
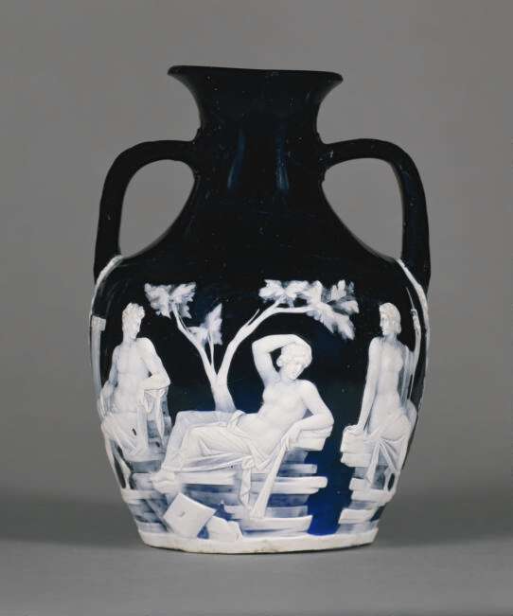
For a considerable number of technical reasons, I believe the Morgan Cup and most of its close relatives among surviving ancient Roman cameo glass vessels were made by glassblowing 5. The group includes a small scent bottle in the J. Paul Getty Museum in Los Angeles (Fig. 17); the Portland Vase (Fig. 18) and the Auldjo Jug, both in The British Museum, London; and a handful of other rare examples.6
The very early dates (roughly 20 B.C.-30 A.D.!) assigned to the group by classical art-history scholars are surprising—no, amazing—considering that glassblowing would have arrived only recently on the Italian peninsula, where these vessels were probably made 7. Video 4 shows a glassblowing process that was essentially the same for all of the vessels cited above. The first part of the video shows the making of a blank for the Getty scent bottle; the second part shows the engraver Max Erlacher skillfully demonstrating the lapidary work (cold working) to create the decoration.
As explained in the preface, following the discovery that molten glass can be inflated, processes had to be invented to exploit that discovery. Videos 4 and 5 demonstrate two such processes, each of which is very different from the other. They offer solutions to the first of two fundamental technical problems that a glassblower of any period faces. The first problem is how to separate the hardened but still very hot glass from the blowpipe. The second problem is how to finish the opening after the inflated glass has been removed from the blowpipe—that is, how to create a finished rim at the opening.
Addressing the question of separating the hardened but still very hot glass from the blowpipe, we must observe that, when glass is gathered on the end of a metal blowpipe and a bubble is blown, their connection is exceedingly strong (Fig. 19, top row). Today, glassblowers use the two-bladed tool called the jacks to create a narrow constriction between the inflated glass and the blowpipe (Fig. 19, bottom row). This is a weak point that can be cleanly and easily broken. I do not believe, however, that this technique was known in the ancient world. I suspect, instead, that it was a development of medieval western European glassworkers.
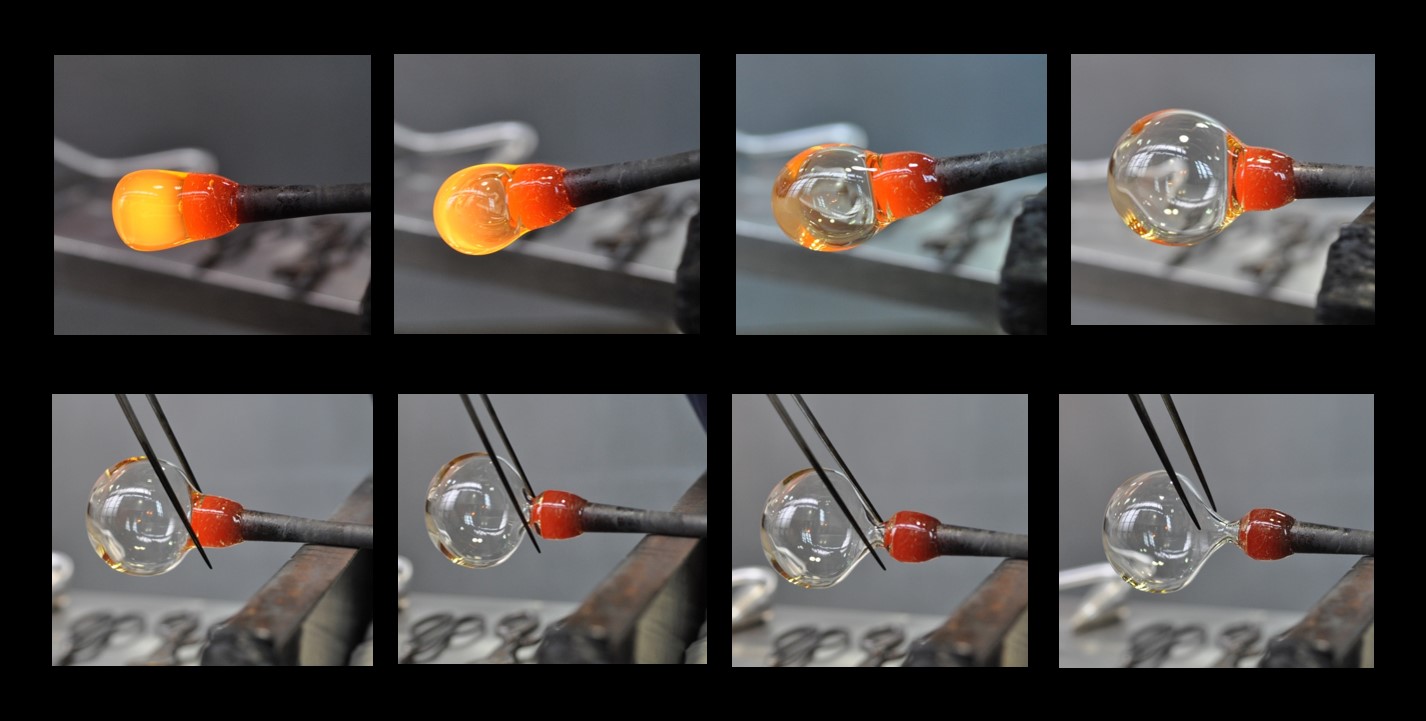
It has been my working theory for a number of years that the invention that made glassblowing reliable and ultimately successful was the practice of forming a tube between the vessel and the blowpipe. Its development might have begun with the workers’ observation that hot glass tubing can be broken cleanly and easily. This section of tubing was made in a number of ways. Two examples follow.
For the small purple-brownish bottle in The Corning Museum of Glass (Fig. 14), the initial inflated glass was elongated to begin forming the tube, and it was lengthened by using a hand tool (Vid. 5). For the Getty scent bottle (Fig. 17), a tube of blue glass was fashioned and then dipped partway into opaque white glass (Vid. 4). When the white glass resoftened the lower half of the tube, the blue and white glasses were inflated together to form the body of the vessel. In both cases, when the moment came to separate the object from the blowpipe, the section of hot glass tubing permitted this to be accomplished easily and predictably—two essential qualities of a successful production process.
The second fundamental technical problem that a glassblower of any period faces is that once the inflated glass has been separated from the blowpipe, how is the rim created and, in many instances, how is the open end of the vessel given its final shape? From the surviving objects, we can see that two basic—and distinctly different—types of rims were made. The first was a furnace-finished rim (Fig. 20). Here, the still-hot vessel was immediately transferred to a tool that enabled it to be held from the base and permitted the reheating and reshaping of the open end. The common practice in ancient workshops was to use a preheated clamp-like tool (Vid. 5) or a metal rod with a little molten glass on its hot end (the punty or pontil) to act as a temporary handle and allow the opening process to take place (Vid. 10). The latter tool left a rough area at the base (a punty or pontil mark), while the former tool did not. Many vessels from the Roman period have doubly strong and attractive folded edges at their furnace-finished rims (Fig. 20].
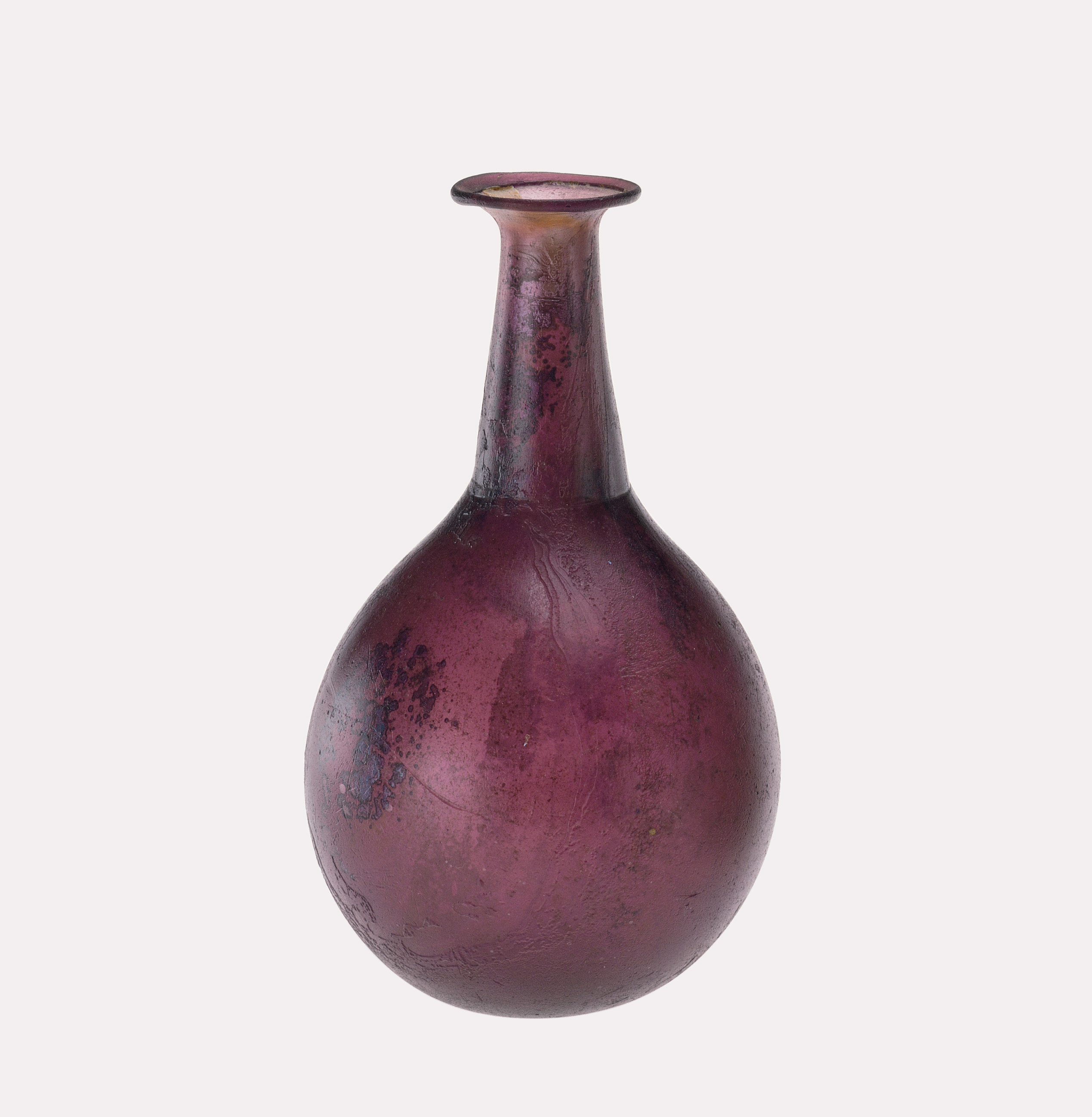
The other basic type of rim seen in ancient blown glass is the cracked-off rim (Fig. 6). Here, the vessel was broken off the blowpipe and immediately placed in an oven for gradual cooling (annealing) to room temperature. When it was cool, the glass was scratched on its outside surface with a sharp tool where the rim was intended to be. Heat was applied in a circular pattern around the glass, and from the rapid expansion of the glass, a crack was formed around the circumference. The resulting edge was exceedingly sharp, and it must have been smoothed by a simple cold-working procedure (Vid. 6). Cracked-off rims have no toolmarks or thickening near their edges, and folded rims cannot be made using this procedure—and, of course, vessels with cracked-off rims never have punty marks.
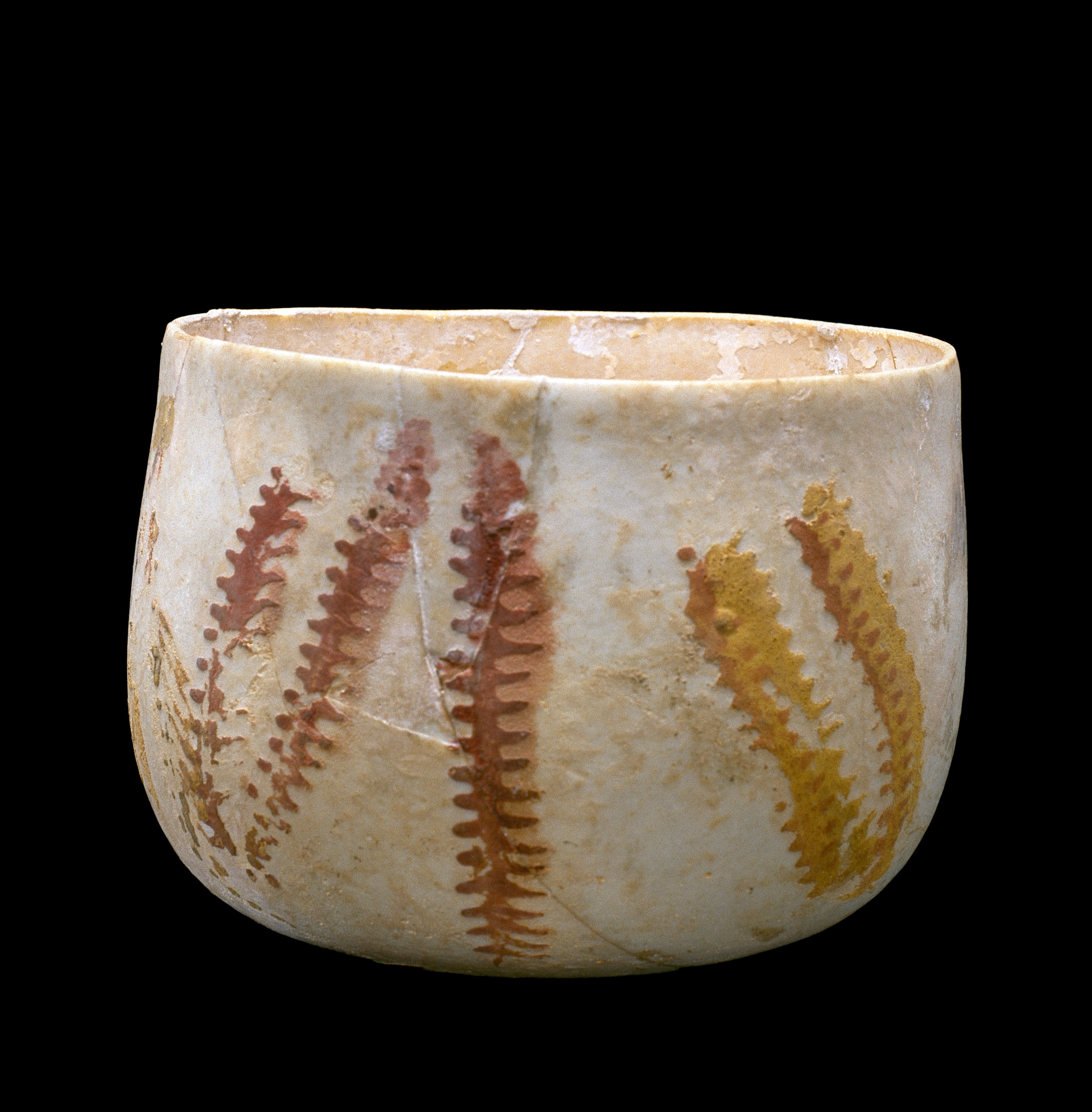
In some ways, creating a furnace-finished rim is the most difficult part of the glassblowing process. Today, only studio glass artists and the most traditional Venetian glassblowers use this technique. In sharp contrast, the cracking-off process requires no specialized skill; just a knowledge of the process and possession of the needed equipment. Today, essentially all commercially made glass—even from the finest houses, such as Baccarat, Riedel, and Lalique—has cracked-off rims. As ancient glassworking technologies were passed down to the present day, cracking off became nearly as ubiquitous as glassblowing itself.
Thus far, we have been considering free-blown glass. In free-blowing, the craftsperson uses the simplest of tools, gravity, centripetal force, and air pressure to shape and control the inflated glass. At some point in the first half of the first century A.D., someone invented another glassblowing process that is still used worldwide today: full-size mold-blowing (Fig. 11). In this process, a partly inflated bubble of glass is lowered into a multipart mold and inflated further, so that it fully occupies the interior. As soon as the glass stiffens to the point of being able to maintain its shape, the mold is opened. The mold nearly instantly sets both the final size and shape of the body of the vessel. The inflated glass is separated from the blowpipe and then given either a furnace-finished or a cracked-off rim (see above). In the video, the object is given a furnace-finished rim with an inner fold (Vid. 7)8. Many objects made by full-size mold-blowing have cracked-off rims (Fig. 22).
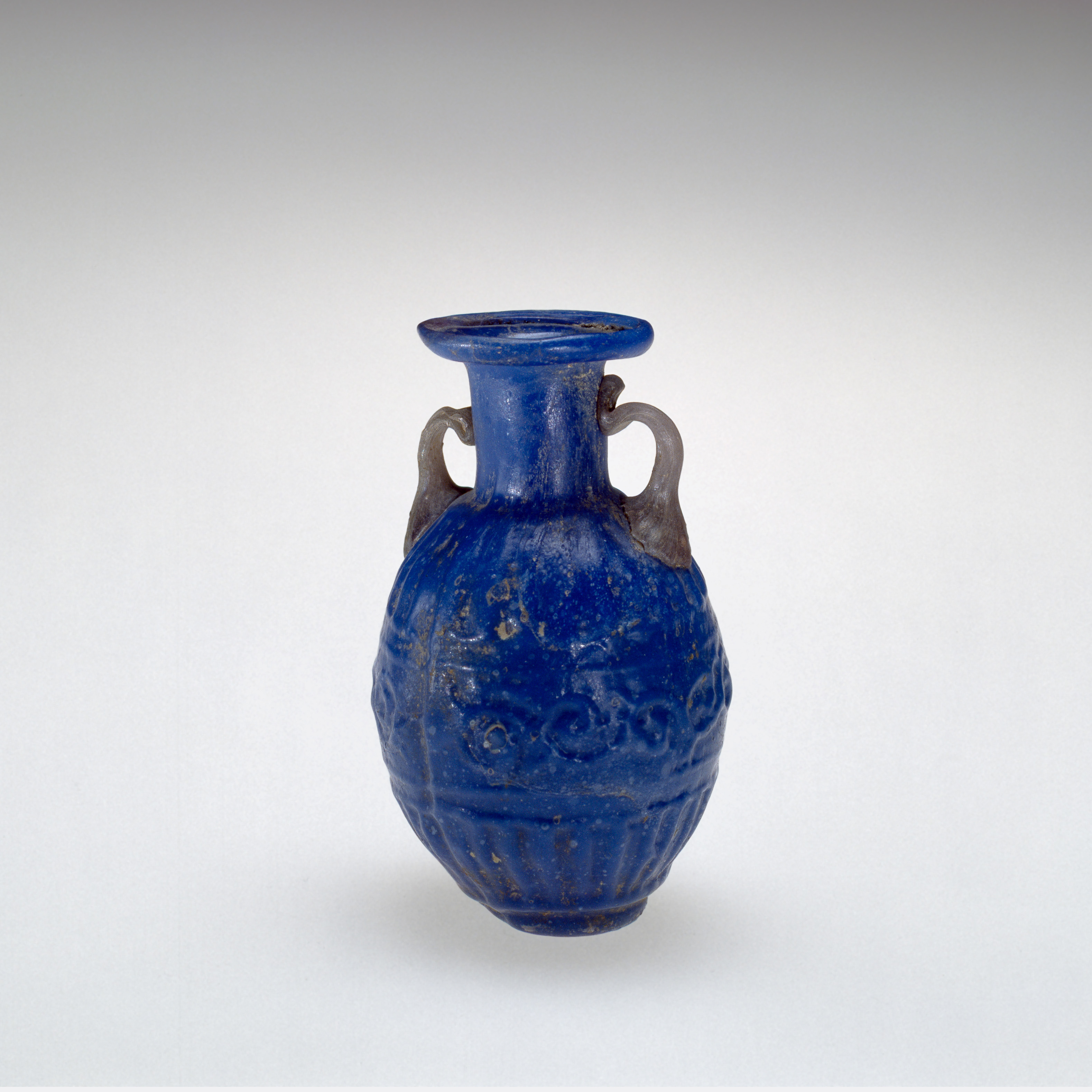
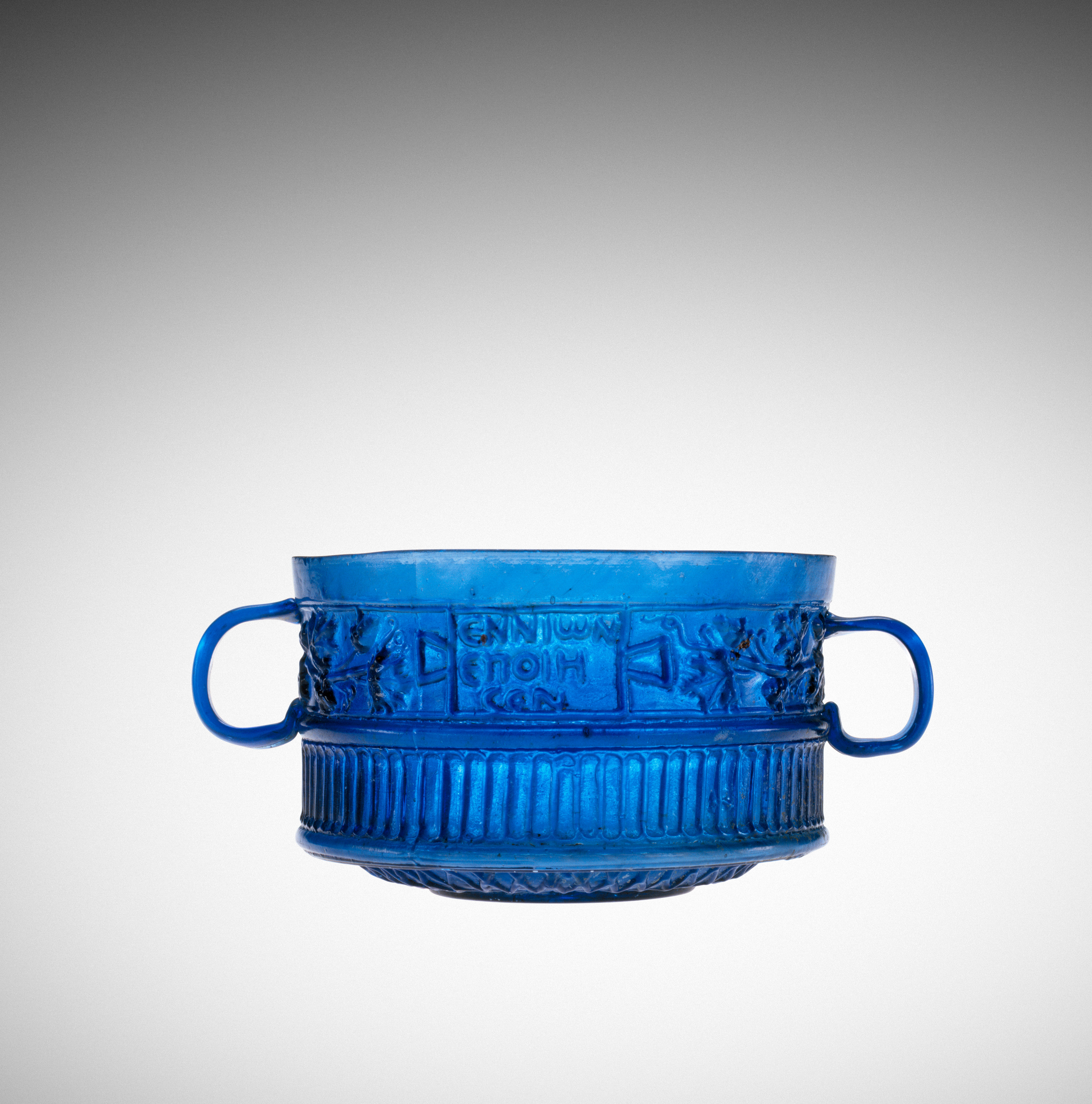
It is hard to overstate the impact that the combining of these two techniques—full-size mold-blowing and cracking off—has had since they were invented some 2,000 years ago. Today, they are employed everywhere in the glass industry. In the ancient world, they were an important part of the making of great numbers of glass vessels that could be afforded by all. In earlier times, glass was used mostly for the making of luxury goods.
Notes
-
For a practical view of the science of glass, see Frank E. Woolley, Glass Technology for the Studio, Corning: The Studio of The Corning Museum of Glass, 1999. ↩︎
-
For a brief but authoritative overview of Roman-period glass, see Veronica Tatton-Brown, “The Roman Empire,” in Five Thousand Years of Glass, pp. 62–97. ↩︎
-
These finds were published in Yael Israeli and Natalya Katsnelson, “Refuse of a Glass Workshop of the Second Temple Period from Area J,” in Jewish Quarter Excavations in the Old City of Jerusalem, Conducted by Nahman Avigad, 1969–1982, v. 3, Area E and Other Studies: Final Report, ed. Hillel Geva, Jerusalem: Israel Exploration Society and Institute of Archaeology, Hebrew University of Jerusalem, 2006, pp. 411–460. ↩︎
-
See Nahman Avigad, Discovering Jerusalem, Nashville: T. Nelson, [1983]. ↩︎
-
William Gudenrath, “How Vessel Blanks Were Made,” in Paul Roberts and others, Roman Cameo Glass in the British Museum, London: British Museum Press, 2010, pp. 25–31. ↩︎
-
Kenneth Painter and David Whitehouse, “Early Roman Cameo Glasses,” Journal of Glass Studies, v. 32, 1990, pp. 138–165. ↩︎
-
Kenneth Painter and David Whitehouse, “Recent Research on the Portland Vase: Style, Date, and Place of Manufacture,” Journal of Glass Studies [note 9], pp. 122–125. ↩︎
-
The most thorough investigation into the practicalities of early full-size mold-blowing processes has been carried out by Mark Taylor and David Hill of Andover, U.K. Their work on the processes used by Ennion is exemplary. See video at https://youtu.be/jaODucearU8?si=SQFeJ8L9-Zsu2UrL. ↩︎